Weighing in Rough Environments: The Role of Capacitive Load Cells in the Meat Processing Industry
Case Study
In the highly competitive and industrially demanding meat processing industry, reliability and cost efficiency are crucial factors for operational success, both when competing locally and globally. Oestergaard A/S, a leading global meat rendering solutions market player, relies on Eilersen digital capacitive load cells for precise and reliable weight measurement—a critical measurement in meat rendering solutions.
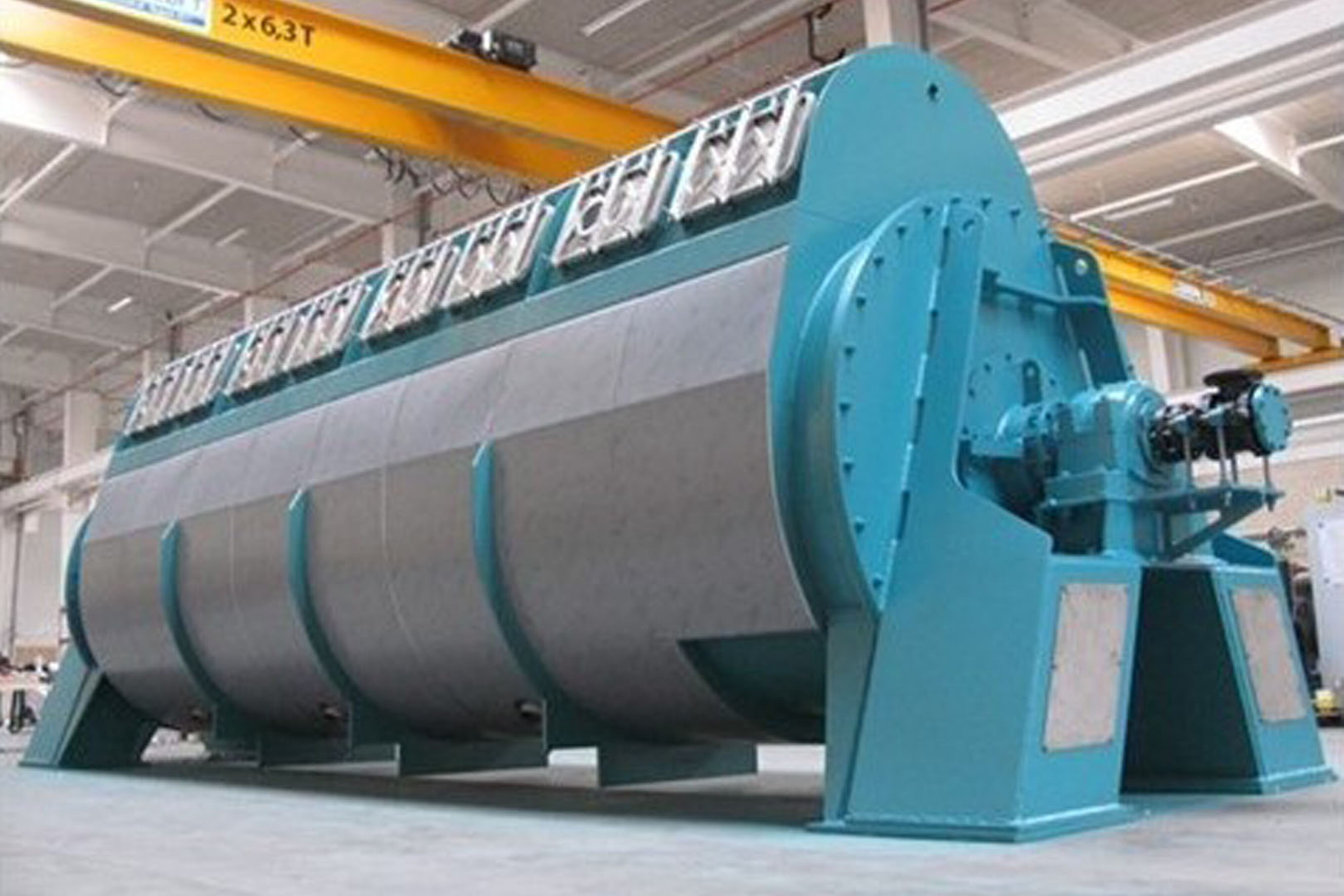
About Oestergaard A/S
Oestergaard A/S has more than 50+ years of experience in developing and managing large manufacturing units for servicing the meat and fish by-products industry, making the Oestergaard family some of the most prominent characters in the rendering industry.
Challenging Environments Drive a Need for Reliable Weighing Solutions
In some industries, the working environment can be exceptionally demanding, and the meat rendering industry is a prime example of this. Anders Juul, who has been a part of this industry for more than two decades, has witnessed firsthand how the technology used in different load cells can impact day-to-day operations.
Operating in meat production facilities can be challenging, with the pervasive presence of ammonia fumes and animal fats on most surfaces. These conditions create a particularly harsh environment for any load cell system and cause load cell cables to disintegrate after a few years. This scenario poses a significant challenge for weighing solutions, emphasizing the need for accurate and robust equipment to endure these tough conditions.
Typically, a meat rendering machine from Oestergaard A/S is installed on four compression load cells and must operate under the following conditions:
- A total working weight of up to 200 tons.
- Internal working temperatures ranging from 40°C to 180°C.
- Horizontal expansion of the machine, of up to 18 mm.
- During installation, it is common to weld on the machines.
The Eilersen capacitive load cells have proven remarkably reliable over the years, with several beneficial features compared to traditional strain gauge load cells. For machines using Eilersen digital load cells, it is possible to monitor the load distribution on each load cell which is beneficial to ensure correct installation. The individual Eilersen digital load cells even send an error code if maintenance should be required for fast and easy trouble-shooting. Beyond these features, the durability of Eilersen load cells seems to impress even customers experienced in weighing technology. Even though it is not recommended, employees at Oestergaard A/S often need to weld on, or close to, machines installed on load cells. Anders Juul, Project Manager at Oestergaard A/S explains:
“Often, welding is required during the installation process, which often damages a strain gauge load cell, causing expensive delays as we need to order express delivery of replacement load cells to customer sites. However, we have not experienced damaging the Eilersen load cells since we started using them many years ago, even when welding on the machines.”
Eilersen load cells installed a decade or more ago - some even 30 years back - have been operating with the same accuracy and reliability as when they were new, despite being exposed to high horizontal loads and frequent overloads.
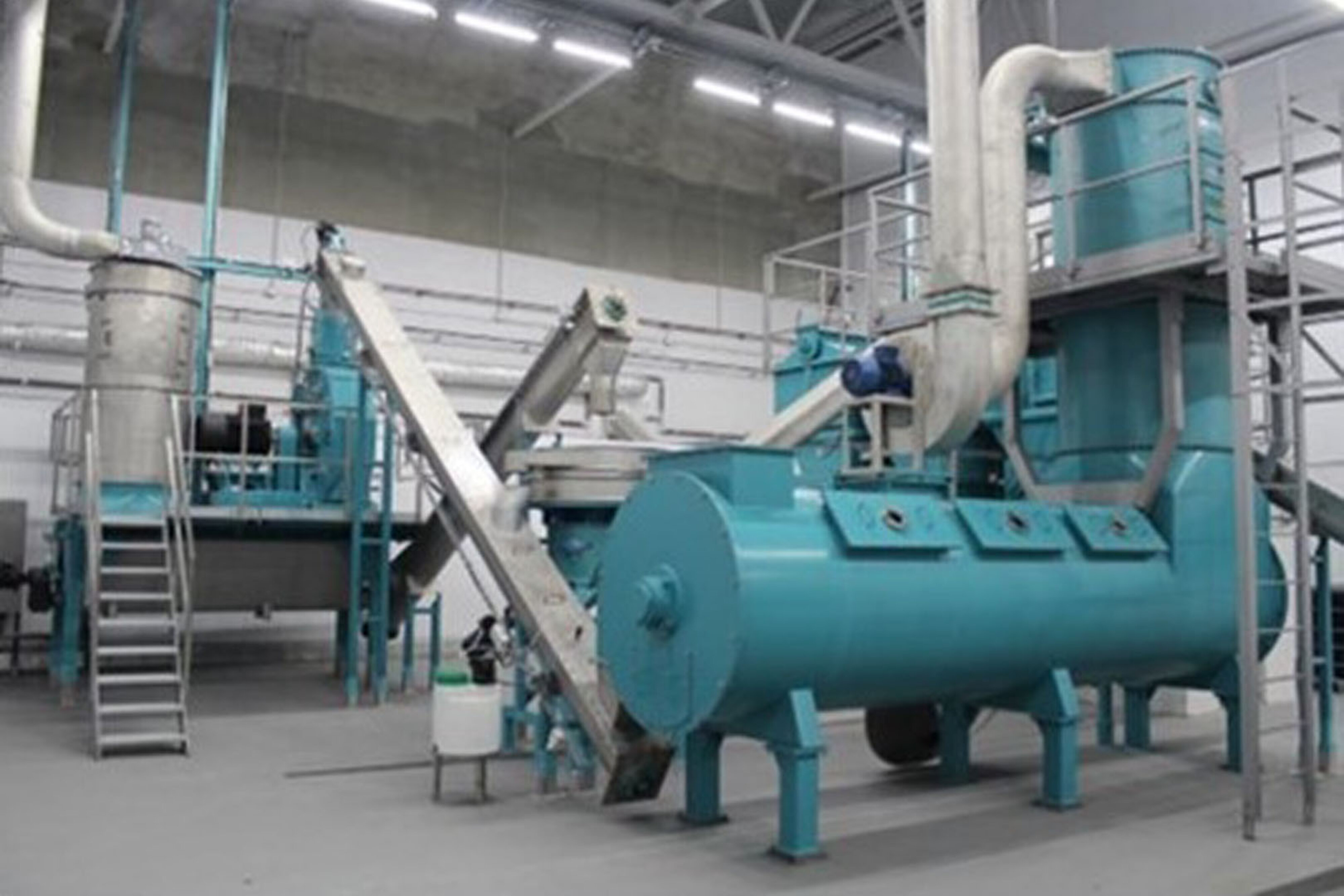
How Oestergaard A/S Reduces Downtime Using Digital Capacitive Load Cells
The ability to replace load cell cables on Eilersen load cells without needing to change or recalibrate the weighing system makes them optimal for harsh meat rendering environments, where load cell cables often have a lifespan of only four to six years. These features, along with their consistent performance over time, not only showcase the exceptional longevity of Eilersen load cells but also their dependability, especially in challenging environments like the meat rendering industry. Anders Juul highlights the advantages of being able to replace load cell cables on-site without the need for recalibration of the system. He shares his experience with Eilersen capacitive load cells, saying:
“We encounter no issues when using Eilersen load cells. Eilersen provides a reliable weighing system that’s not only a breeze for us to work with, but also instills confidence in our customers who rely on the load cells in day-to-day operations. From planning to installation, the process is always smooth sailing. If something goes wrong after commissioning, and we need to replace a load cell cable, we can easily do so without replacing the entire load cell.”
Expertise as a Service
In the meat rendering industry, everything must go according to plan—always. But sometimes, unforeseen issues arise, and quick action and support is necessary. Anders is confident that there won’t ever be such an incident when using Eilersen. However, when Oestergaard A/S needs any assistance, expertise and first-class support is always available as a service.
“If we ever need help, we just pick up the phone and call Eilersen. I’m only one phone call away from talking to someone who understands the situation and can help solve any issue. Having access to such expertise is critical for my role and our clients.”
Oestergaard A/S and Eilersen have collaborated for more than five years on numerous projects. If you are a supplier in this sector, please give us a call, and together, we make a substantial difference for your clients – and your business.
Summary
- A meat rendering machine can have a horizontal expansion of up to 18 mm with a working weight of up to 200 tons.
- Eilersen load cells installed 30 years back are still operating with the same accuracy and reliability.
- The ability to replace cables without recalibration is a significant benefit for Oestergaard A/S, as cables often fail after four to six years due to the harsh environment.
- Anders Juul, Project Manager at Oestergaard, emphasizes the reliability, ease of use, and digital benefits of Eilersen load cells.
Request a Quote
Looking for a tailored weighing solution? Fill out the form below, and our experts will provide you with a customized quote based on your specific needs. Whether you're in food, pharma, or another industry, we'll help you find the perfect solution.
Get started today
Complete the form, and we’ll get back to you promptly with a competitive quote and expert guidance to fit your requirements.