The Choice for Industrial Applications
The Eilersen digital capacitive technology is based on a non-contacting ceramic sensor mounted in a low stressed load cell body. As the load cell contains no moving parts and the ceramic sensor is not in contact with the load cell body, the load cell tolerates very high overloads, sideloads, torsion and welding voltages.
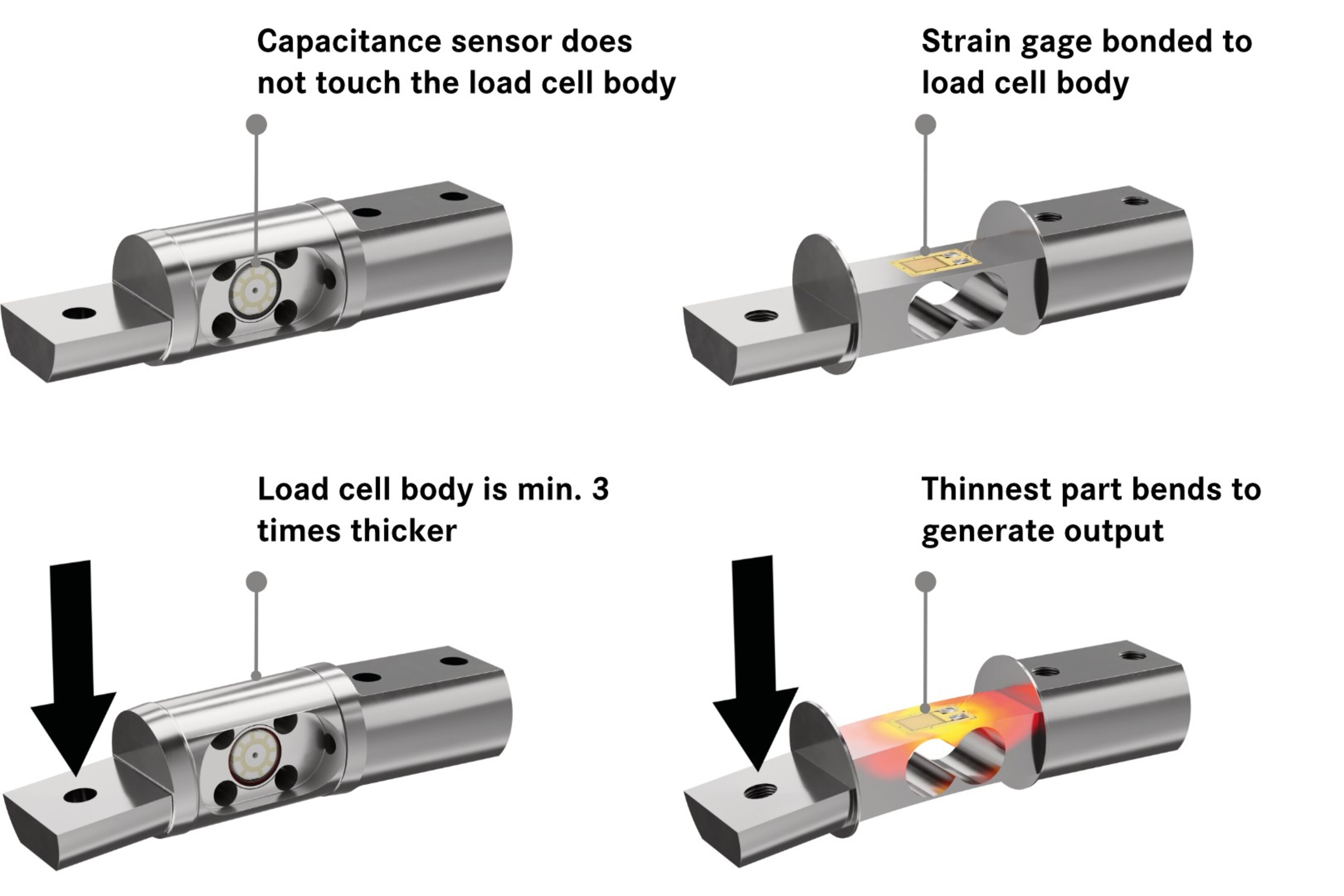
Accurate and Reliable
Hygienic and Easy to Clean
Robust Design
Simple and Hygienic Installation
This robust technology allows for a very simple and hygienic mechanical installation of the Eilersen load cells without expensive and complicated mounting kits, stay rods or overload protection devices. The simple installation eliminates the need for maintenance and reduces the total cost of ownership.
The True Digital Weighing Solution
The electrical installation of the Eilersen digital load cells is pure plug-and-play as the proprietary ASIC in the capacitive load cells generates a digital signal which is compensated and calibrated in the load cell.
The output from the Eilersen digital load cells contains the measuring data and is compensated to ensure the highest accuracy (up to OIML C6 MI10 or 99.99% of rated capacity) and quality on the market.
Flexible Connectivity
The Eilersen proprietary design results in unsurpassed flexibility, fast communication and allows for connection to a wide range of equipment, fieldbus interfaces and outputs (PLCs, PCs, SCADA systems, Weighing Terminals, PROFINET, EtherCAT, EtherNet/IP, Modbus TCP/IP, RS485, 4-20mA, 0-10VDC etc.).
Easy Commissioning and Service
The pre-calibration of the Eilersen load cells and the possibility to monitor the load and status of each individual digital load cell, provides visibility, easy troubleshooting and saves time during commissioning.
Furthermore, the load cell cables can be replaced on-site if required, and the cable length (up to 100 meters) has no influence on the load cell calibration
Patented and Trusted Worldwide
The capacitive technology and mechanical design applied in the Eilersen load cells is patented, and trusted by customers in more than 90 countries worldwide.