Digital capacitive and strain gage load cell technology compared
The basics
Capacitive and strain gage load cells both rely on an elastic element which is deformed by the load to be measured.
The material used for the elastic element is typically aluminum for low-cost load cells and stainless steel for load cells used in corrosive industrial applications.
Eilersen’s capacitive load cells are capable of greater accuracy and sensitivity than strain gage load cells. Furthermore, the sensor in capacitive load cells generates a signal based on the deformation of an elastic element (the load cell body) without being in contact with the elastic element. In contrast, strain gage load cells generally employ an insulated resistance foil that is bonded directly to the elastic element (the load cell body). The physical separation of the capacitive sensor from the elastic element makes our capacitive load cells far more durable and resistant to damage from shocks and overloads.
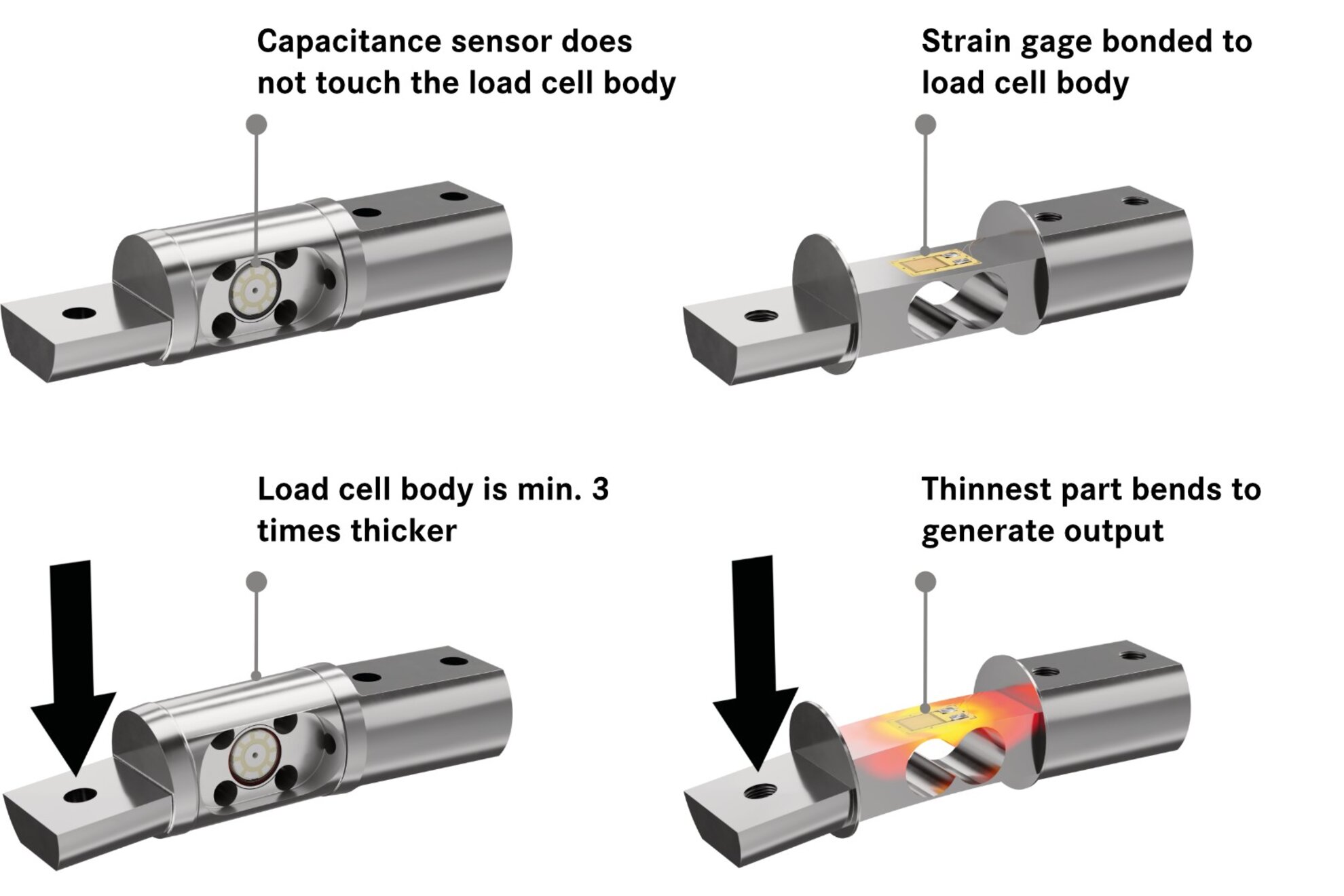
Comparison - Capacitive and Strain Gage Load cells
Sensitivity
Capacitive sensors are very sensitive with a change of capacitance of up to 10%, while the foil strain gage typically only has a change of resistance of 0.1%.
Because of the higher sensitivity of capacitive sensors, a much lower deformation of the elastic element is needed. The strain on the elastic element of a capacitive load cell is, therefore around 5 to 10 times lower than that of an elastic element for a strain gage load cell.
The reduced strain on the elastic element, combined with the fact that a capacitive sensor is non-contacting, provides the capacitive load cell with much higher shock resistance and overload capability than strain gage load cells.
Cabling and sealing
The high change of capacitance permits the Eilersen capacitive load cells to provide a high-speed digital output signal, representing the load directly in g, kg or Newtons.
A low-cost coaxial cable with a one-wire hermetically sealed connector supplies the load cell with power and transmits the high-speed digital signal back to the instrumentation, which may be placed several hundred meters away.
In a standard analog strain gage load cell, the power supply and the low-level analog signal are normally conducted through a 6-wire cable to the instrumentation where the analog signal is converted to a digital signal.
In a digital strain gage load cell, an amplifier and the A/D converter are placed in the housing or load cell body and the power supply and the digital signals are normally conducted through a 6- or 7-wire cable to the instrumentation.
With the 6 or 7 wire cables used in strain gage load cells, it is difficult to obtain the necessary IP68 protection for industrial environments without complicated water traps or multi-pole hermetic feed through connections.
In contrast to this, the uncomplicated IP68 single-pole connector used in the Eilersen capacitive load cells, has the logistically valuable advantage that the cable may be mounted just before delivery, with length and PVC/Teflon type tailored to customer specifications.
Conclusion
The Eilersen capacitive load cell provides a tolerance to shock and overloads of up to 10 times the nominal load, as compared to the 2 times nominal load for strain gage load cells.
This is an obvious advantage in industrial environments and especially for lower-capacity load cells, where the risk of damage because of shocks and overloads is high.
The Eilersen capacitive load cell provides a tolerance to sideloads and eccentric loads of up to 10 times higher than possible with strain gage load cells
These features mean that expensive mounting kits with sideload- and overload stops, which are inconvenient and often cost as much as the load cell itself and require additional maintenance, are not needed with the Eilersen capacitive load cells.
The factory-calibrated digital high-speed signal, conducted through the well-shielded coaxial cable, provides simple plug-and-play installation, as well as EMC protection and protection against welding voltages.
The high-speed signal is sent at 230 kBaud with the load value in 24 bits and with address and diagnostic codes. This enables the 1000+ readings/second required in dynamic weighing applications and meets the very short update time of 2 mS necessary for four loads cells in platform and cargo weighing, mixing, dosing and hopper applications.
As a final conclusion, the Eilersen capacitive load cells have important advantages compared to the digital strain gage load cells, which are still just strain gage load cells.